There are a variety of defects that may be encountered during the valve welding process, and these defects, if not addressed in a timely manner, may have a serious impact on the performance and safety of the valve. The following are some common valve welding defects and their treatment methods, designed to help readers better understand and cope with these problems.
First, the treatment of porosity
Definition of porosity: Porosity is the failure of the gas in the molten pool to escape in time during welding, resulting in the formation of cavities in the weld.
Treatment method:
Surface porosity: use an abrasive wheel or wire brush to gently grind off the weld metal around the porosity until a clean metal surface is exposed. Subsequently, use manual arc welding or gas shielded welding to make up the weld. When making up the weld, increase the welding current appropriately to ensure that the weld metal has enough melting depth so that the gas in the gas hole can escape smoothly.
Internal porosity: First, use non-destructive testing techniques to determine the location and size of the porosity. Then, the weld metal where the porosity is located is removed using carbon arc gas planing or machining methods until a porosity-free metal layer is exposed. Next, follow a filler welding process similar to that for surface porosity, but with stricter control of weld quality to prevent recurrence of porosity.
Second, slag treatment
Definition of slag: slag is the slag remaining in the weld after welding.
Treatment methods:
Surface slag: use grinding wheel or wire brush to remove the slag, and make-up welding. Before rewelding, make sure the bevel is clean and free of impurities, and adjust the welding process parameters to ensure that the weld metal is well fused with the base material.
Internal slag: For shallow slag, carbon arc gas planing can be used to remove; for deeper slag, drilling may be required to remove it. After removing the slag, make-up welding. In the process of replenishment welding, pay attention to control the welding heat input to avoid overheating leading to the deterioration of the weld organization.
Third, crack treatment
Crack definition: crack is one of the most serious defects in valve welding, which can be divided into hot crack, cold crack and reheat crack.
Treatment method:
Hot cracks: use the grinding wheel to polish off the superficial hot cracks until the metal surface without cracks is exposed. For deeper thermal cracks, it is necessary to excavate the cracks and then perform filler welding. Preheat the gouged area before refinishing and apply a slow cooling treatment after refinishing.
Cold Cracks: Cold cracks are thoroughly inspected and analyzed to determine the direction and depth of the crack. For shallow cold cracks, remove them by grinding and refill welding; for deeper cold cracks, it may be necessary to drill holes to stop the cracks, dig out the cracks and then refill welding. Strictly control the welding heat input and interlayer temperature in the process of refilling welding, and carry out heat treatment after welding to eliminate residual stress.
Reheat cracks: Try to avoid welding and heat treatment under conditions that are prone to reheat cracks. For the reheat cracks that have appeared, remove the cracks after rewelding, and optimize the welding process according to the characteristics of the steel. Post-weld heat treatment, reasonable control of the heating rate, holding time and cooling rate.
Fourth, unfused and unwelded processing
Definition of unfused: between the weld metal and the base metal or weld metal between the layers are not completely melted combination.
Unwelded definition: the root of the welded joint is not completely fused.
Treatment:
Unfused: For surface unfused, use an abrasive wheel to grind off the unfused area and reweld. Ensure sufficient heat input during re-welding to fully melt the base metal and filler metal. For internal non-fusion, use non-destructive testing to determine the location and then remove the non-fused part before re-welding.
Unwelded through: The treatment method is similar to the internal unfused, first determine the position by non-destructive testing to remove the un-welded through parts and then make-up welding.
V. Other Precautions
Professional operation: the processing of valve welding defects should be carried out by professionals to ensure the quality and safety of processing.
Strict testing: After processing, the weld is strictly tested, including appearance inspection and non-destructive testing to ensure that it meets the requirements for use.
Preventive measures: In order to reduce the occurrence of valve welding defects, preventive measures should be taken, such as optimizing the welding process, selecting suitable welding materials and equipment.
Through the above guidelines, we hope to help readers better understand and respond to the problem of valve welding defects to ensure the safety and performance of the valve.
Valve welding defects treatment guide
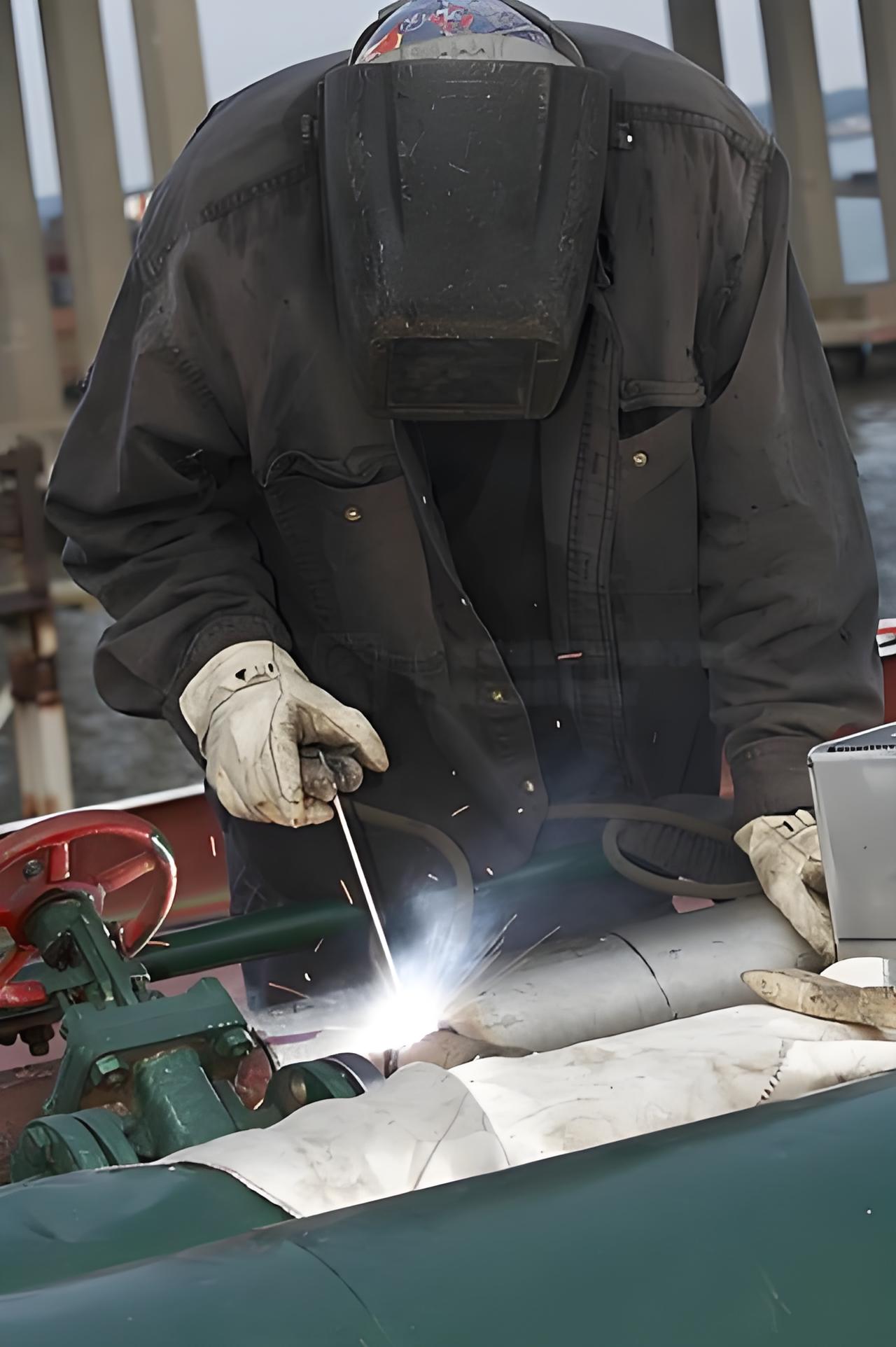