Among pressure-bearing valves for industrial pipelines, cast steel valves are popular for their cost-effectiveness and design flexibility. However, due to the complexity of the casting process, cast steel valves may suffer from casting defects such as sand holes, porosity, cracks, etc., which pose a threat to the performance and safety of the valves. Therefore, it is crucial to understand and master the patching technology of cast steel valves.
First, cast steel valve defects
Defects judgment
In production practice, some casting defects are not allowed to fill welding, such as penetrating cracks, penetrating defects, can not remove the sand and slag as well as the area is too large shrinkage and so on. Before welding, the type of defects must be accurately judged.
Defect Rejection
Casting defects are usually removed by carbon arc gas planing or carbon steel welding rod with high current, and then the defective parts are polished to a metallic luster with an angle grinder. To ensure the quality of the filler weld, the defects should be removed completely.
Preheating of defective parts
For carbon steel and austenitic stainless steel castings, filler welding area is small, shallow depth, generally no preheating. But pearlite steel castings such as ZG15Cr1Mo1V, ZGCr5Mo, etc., due to the tendency to harden, cold welding easy to crack, should be preheated, preheating temperature of 200 ~ 400 ℃.
Second, filler welding method
Replacement welding requirements
Austenitic stainless steel castings, filler welding should be carried out in a ventilated place for rapid cooling. Pearlite low alloy steel castings and refill welding area of carbon steel castings should be avoided rapid cooling to prevent cracks. The flux slag should be removed immediately after refill welding, and the refill welding area should be evenly hammered to reduce the refill welding stress.
Welding rod processing
Before refinishing, the welding rod should be checked whether it is preheated and dried. The welding rod should be dried at 150-250°C for 1 hour and placed in a holding tank for backup. If the surface of the welding electrode is peeled, cracked or rusted, the electrode should be replaced with a new one.
Replacement welding times
Pressure castings such as valve shell by the test pressure seepage, the same part of the general only allowed to make-up welding once. Multiple filler welds will make the steel grain size, affecting the casting pressure performance. Non-pressure castings of the same part of the number of filler welds generally not more than 3 times.
Welding layer height
The height of the filler layer of the casting should be generally higher than the casting plane about 2mm, in order to facilitate subsequent machining. Mending welding layer is too low easy to reveal the welding scar, too high is time-consuming and costly material.
Third, after welding treatment
Important patch welding treatment
Hydrostatic test leakage of castings, patch welding area is larger or deeper castings are regarded as important patch welding. For this kind of important patch welding, should be de-stressing treatment or complete re-heating treatment. However, many defects are discovered during the finishing process and can no longer be fully reheated. Therefore, they are usually solved in the field by experienced welders using effective methods.
Stress Relief
Defects found after finishing can be stress relieved by localized heating and tempering with an oxy-acetylene flame. Heat until a dark red color appears on the surface of the casting (about 740°C), keep warm for a period of time and immediately cover with asbestos sheet for slow cooling.
Non-destructive testing
For heavy defects and important patch welding, effective non-destructive testing, such as magnetic particle inspection or radiographic inspection, must be carried out to prove that the quality of the patch welding is qualified.
Grading
Grade assessment of defects in the patch welding area should be carried out in accordance with relevant standards. For cast steel valves and patch welding areas of power station valves, the rating shall not be lower than the third level in GB/T5677-1985. For acid and corrosion resistant pipelines and high pressure cast steel valves with shell pressure-bearing parts, the rating shall be higher.
Hardness test
After the patch welding area is qualified by non-destructive testing, if machining is required, hardness testing should also be carried out. Too high hardness in the rewelded area may lead to tool chipping and localized stress concentration. Therefore, the hardness of the filler weld area should be similar to that of the cast steel part itself.
Conclusion
The scientific patch welding of defects in cast steel parts is an energy-saving remanufacturing engineering technology. With the support of modern testing means, the patching welding tools, welding materials, personnel and processes should be constantly innovated and improved to realize the integration of manufacturing and repair. The performance and safety of cast steel valves can be ensured and their service life can be prolonged through scientific patching welding technology.
Valve welding defects how to deal with?
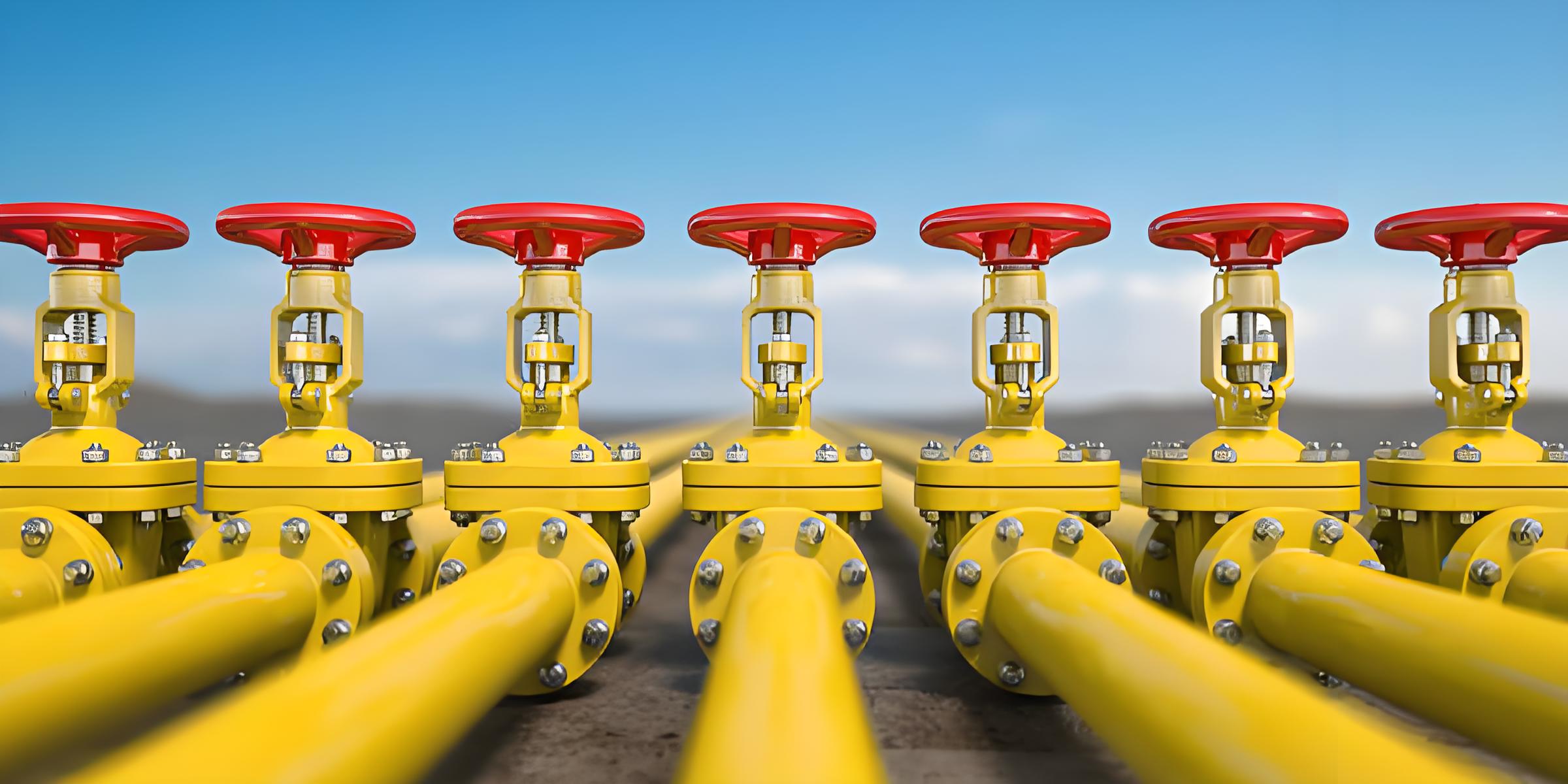