A detailed inspection is essential before valve installation to ensure that the valve meets design requirements and operates safely. The following is a series of checking steps for the valve before installation:
Model and specification confirmation: double-check the model and specifications of the valve to ensure that they are exactly the same as the requirements on the engineering drawings.
Flexibility test: Check whether the valve stem and valve opening is smooth, no jamming or skewed phenomenon.
Appearance check: Make sure the valve is not damaged, especially the threaded part of the threaded valve, which must be square and intact.
Firmness of connection: Check whether the connection between valve seat and valve body, valve flap and valve seat, valve cover and valve body as well as valve stem and valve flap is firm.
Material suitability: ensure that the valve gasket, packing and fasteners (such as bolts) suitable for the nature of the working medium.
Old Valve Disposal: For pressure reducing valves that have not been used for a long period of time, disassemble and clean them to remove debris such as dust and grit.
Sealing verification: Remove the through-port capping and check the degree of sealing of the valve flap to ensure that the valve flap can close tightly.
Pressure test of the valve:
Strength test: carried out in the open state of the valve, the test pressure is usually 1.5 times the nominal pressure (for valves with PN ≤ 32MPa), lasting for at least 5 minutes, to check whether there is any leakage on the outer surface of the valve.
Tightness test: in the valve completely closed state, the test pressure is usually nominal pressure or 1.25 times the working pressure (depending on the type of valve), to verify whether the valve sealing surface leakage.
General principles of valve installation:
Position selection: valve installation location should be avoided to hinder the operation, disassembly and maintenance of equipment, piping and the valve body itself, while considering aesthetic.
Valve stem direction: valves on the horizontal pipeline, the valve stem should be installed towards the top or tilt to avoid handwheel down. For valves on overhead pipelines, the valve stem and handwheel can be installed horizontally and operated remotely by chain.
Arrangement and height: the valves should be arranged neatly and beautifully, and the handwheels of the valves on the risers should be flush with the chest height (about 1.0-1.2 meters) for easy operation.
Spacing requirements: side-by-side risers on the valve centerline elevation should be the same, the net distance between the handwheel is not less than 100 mm; side-by-side horizontal piping on the valve should be staggered installation.
Bracket and platform: when installing valves on heavy equipment (such as pumps, heat exchangers), a bracket should be set up; frequently operated and high position of the valve, a fixed operating platform should be set up.
Flow direction indication: valves with arrow symbols, should ensure that the arrow pointing to the same direction of flow with the media in the pipeline.
Flange and threaded installation: when installing flanged valves, ensure that the two flanges are parallel and concentric; when installing threaded valves, they should be equipped with a live joint to facilitate disassembly.
Valve installation precautions:
Valve material is mostly cast iron, fragile, avoid heavy impact.
Carrying light to put, lifting rope should be tied to the valve body, avoid chained to the handwheel, valve stem or flange bolt holes.
The valve should be installed in a location that is easy to operate, maintain and overhaul, and avoid burying into the ground.
Ensure that threads are intact and that suitable sealing material is used.
When installing flanged valves, tighten connecting bolts evenly.
Valves should be kept closed during installation, and when the valve stem valve flap needs to be disassembled under special circumstances, it should be operated in the open state first.
Installation of commonly used valves:
gate valve: no directional requirements, but can not be installed upside down, mostly used for fully open or fully closed operation.
Globe valve: the installation of the fluid flow direction, follow the “low into the high out” principle.
check valve: to prevent reverse flow of media, installation, also pay attention to the direction of flow.
Pressure Reducing Valve: Installation should be vertical and the arrow pointing to the direction of flow of the medium, equipped with shut-off valves, pressure gauges and other accessories.
Traps: Used in steam systems to discharge condensate, air and carbon dioxide, and are categorized into mechanical, thermostatic and thermodynamic types according to their operating principles.
safety valves: Used to control the pressure not to exceed the specified value, to protect equipment and personal safety, the installation needs to be vertical and before and after the cut-off valve shall not be set (except in special circumstances), the discharge pipe should be led to the outdoor safety zone.
By following the steps and principles detailed above, you can ensure that your valves are properly installed and operate efficiently to meet U.S. engineering standards and safety requirements.
Valve Inspection and Installation Guide
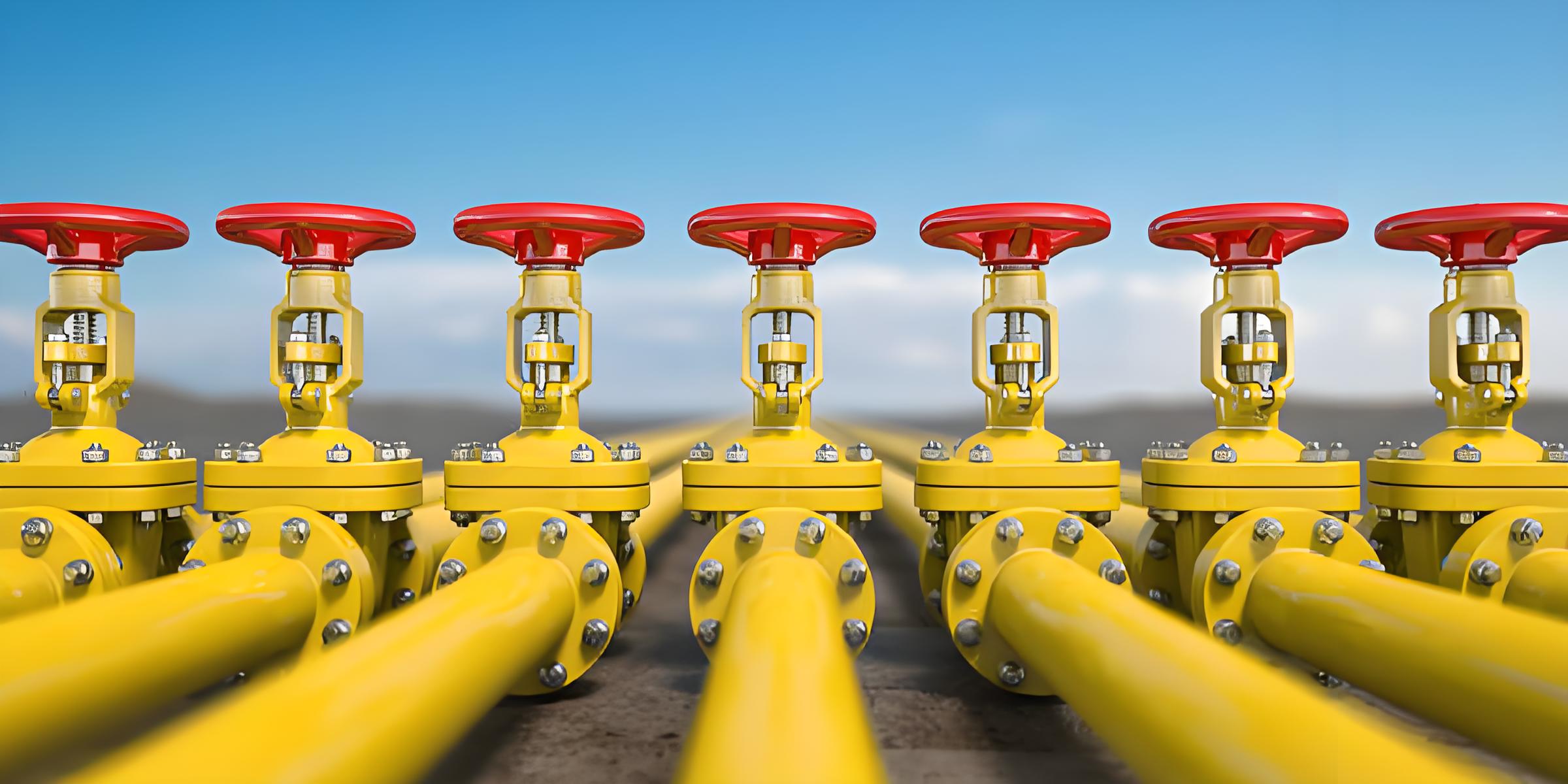