Valve as a key component in the fluid control system, its anti-corrosion performance is directly related to the stability and safety of the system. In order to ensure the long-term stable operation of valves, we need to pay attention to the internal and external corrosion protection measures of valves. The following is a guide to valve corrosion prevention for U.S. readers, designed to introduce the knowledge and practice of valve corrosion prevention in an easy-to-understand way.
First, the valve internal corrosion prevention
Valve internal corrosion is mainly concerned with the valve cavity and the media contact surface, the purpose is to prevent the medium to the valve internal corrosion. The following are several common internal anti-corrosion measures:
Selection of materials according to the characteristics of the medium:
When selecting valve materials, we need to consider the characteristics of the medium, such as corrosivity, temperature and pressure.
For strong corrosive media, stainless steel and alloy steel and other corrosion-resistant materials are ideal.
Coating protection:
A layer of anti-corrosion paint is applied to the inner cavity of the valve, which can form a protective film and isolate the medium from direct contact with the inner cavity of the valve.
The choice of anti-corrosion paint should be based on the characteristics of the medium and the use of the environment to determine to ensure its effectiveness.
Optimize the design:
The occurrence of corrosion can be reduced through reasonable valve structure design and processing technology.
For example, design details such as avoiding stress concentration and reducing welded joints can reduce the risk of corrosion.
Second, the valve external anti-corrosion
Valve external anti-corrosion is mainly concerned about the valve shell and connecting parts of the anti-corrosion, in order to prevent the external environment on the valve caused by corrosion. The following are several common external anti-corrosion measures:
Surface cleaning and treatment:
Mechanical descaling: use sandpaper, wire brushes and other tools to clean the surface of the valve to remove rust and dirt.
Sandblasting: use compressed air to spray abrasive at high speed onto the valve surface to remove dirt and oxidized layer, and improve the roughness and adhesion of the surface.
Coating protection:
Spraying anticorrosion paint: spray a layer of anticorrosion paint on the valve surface to form a protective film, isolating the valve body from oxygen and moisture in the air.
Plastic spraying: spray plastic powder evenly on the metal surface of the valve, after high temperature baking to form a dense coating.
Electroplating: Plating a layer of corrosion-resistant metal on the surface of the valve, such as chrome-plated or nickel-plated to enhance the corrosion resistance of the valve.
Add a protective layer on the outside:
Installation of protective cover: install plastic cover, rubber cover and other protective cover on the outside of the valve to isolate the valve body from direct contact with the external environment.
Winding anticorrosive tape: Wind a layer of anticorrosive tape on the surface of the valve, such as polyethylene anticorrosive tape or glass wire tape, to form a protective layer.
Electrochemical protection:
Anodic protection: By applying anodic current to the protected metal, a passivation film is formed on its surface, thus preventing the occurrence of corrosion reaction.
Cathodic protection: by applying current to make the valve become the cathode of the corrosion battery, thus avoiding corrosion. This method is particularly suitable for buried or underwater use of the valve.
Regular maintenance:
Regularly overhaul the valve to check whether there is corrosion, wear and tear and other problems, and timely treatment.
Regularly clean the dirt and corrosion products on the surface of the valve to keep its surface clean and smooth.
Environmental control:
Where possible, the corrosion process can be slowed down by controlling factors such as temperature, humidity and oxygen concentration of the environment in which the valve is located.
For example, the use of open plant or ventilation and cooling measures to reduce the ambient temperature and humidity.
Through the implementation of the above measures, we can effectively improve the corrosion resistance of the valve to ensure its long-term stable operation. We hope that this valve anti-corrosion guide can provide practical reference and help for American readers.
Valve corrosion guide: internal corrosion and external corrosion comprehensive analysis
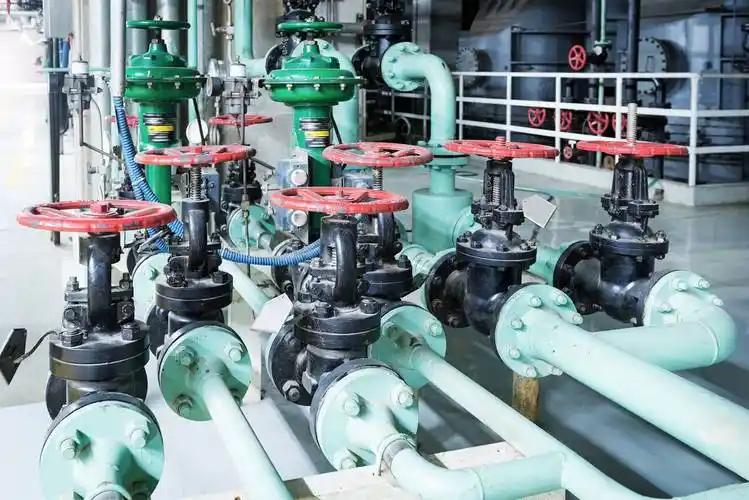