Selection factors for control valves I. Selection of valve type
Determine the nominal pressure: Do not select the nominal pressure (PN) based on the maximum pressure (Pmax) alone. Rather, it should be combined with the temperature, pressure and material of the three conditions, from the relevant tables to find the appropriate PN value, and ensure that the selected valve PN value to match.
Meet leakage requirements: Ensure that the leakage of the selected valve type meets the process requirements.
Working differential pressure: the working differential pressure of the selected valve should be less than its allowable differential pressure. If it is not satisfied, it needs to be considered from a special point of view or choose other types of valves.
Temperature range: the temperature of the medium should be within the operating temperature range of the valve, while the ambient temperature should also meet the requirements.
Anti-blocking design: According to the cleanliness of the medium, consider the anti-blocking design of the valve.
Corrosion resistance: according to the chemical nature of the medium, select the valve with the appropriate corrosion resistance.
Erosion and wear resistance: consider the differential pressure and hardness of the medium, select the valve can resist erosion and wear.
Cost-effective: comprehensive consideration of performance, price and maintenance costs. Priority is given to valves with simple structure, easy maintenance and easy availability of spare parts; while considering service life and price.
Preferred order: butterfly valves, single-seat valves, double-seat valves, sleeve valves, angle valves, three-way valves, ball valves, eccentric rotary valves, diaphragm valves, etc., according to the specific needs of the selection.
Second, the choice of actuators
Pneumatic thin-film type: the simplest and commonly used type of actuator.
Electric type: Although the driving source (power supply) is convenient, the price is higher, and the reliability and waterproof performance are not as good as pneumatic actuators. Therefore, pneumatic actuators are preferred where possible.
New electric actuators: Although more expensive, they offer higher reliability and accuracy and are suitable for applications with higher control requirements.
Piston actuator: there are various specifications to choose from, but you should avoid choosing models that are too large or too heavy to reduce the burden of installation and maintenance.
Third, the choice of materials
Valve body material: should meet the requirements of the process connection pipeline, including pressure resistance level, use of temperature and corrosion resistance.
Avoid cast iron valve: for water vapor, wet gas and flammable and explosive media, as well as ambient temperatures below -20 ℃ occasions, it is not suitable for cast iron valve.
Wear-resistant materials: in the vapor corrosion, erosion of serious media, should be selected wear-resistant materials such as cobalt-based alloys or Stryker alloy.
Corrosion-resistant materials: according to the type of medium, concentration, temperature and pressure, select the appropriate corrosion-resistant materials.
Lining materials: the selection should take into account the temperature, pressure and concentration of the working medium, and to ensure that the valve action will not cause physical or mechanical damage.
Fourth, the choice of flow characteristics
According to the specific needs of the selection of appropriate flow characteristics, such as logarithmic characteristics or linear characteristics. Detailed selection can refer to specialized information.
Fifth, the role of the choice of mode
Failure open/close: consistent with the U.S. representation, i.e., failure open corresponds to gas-closed valves, failure close corresponds to gas-open valves.
Spring range: When selecting the spring range, the need for the output force to overcome the unbalance force needs to be considered. In case of difficulty, consult the manufacturer for assistance in calculation and adjustment.
Sixth, the choice of flow direction
Flow open and flow closed: Understand the impact of the flow direction of the medium on the performance of the valve, and select the appropriate flow direction as needed.
Small diameter valves: for small diameter valves (such as dg ≤ 15), especially high-pressure valves, optional flow closed to improve life.
Selection of packing
PTFE packing: small friction but limited temperature resistance, relatively short life.
Graphite packing: large friction but good temperature resistance, long life. Graphite packing is recommended for valves with high temperature and positioner.
Eight, the choice of accessories
Common accessories: including positioners, converters, relays, booster valves, holding valves, pressure reducing valves, filters, oil mist, travel switches, position transmitters, solenoid valves and handwheel mechanism.
Necessity: Select the necessary accessories according to the actual needs and avoid unnecessary additions to increase the price and reduce reliability.
Positioner: Although it can improve the output force and speed of action, it is not necessary for all occasions.
Converter: For fast response systems, a converter can be selected to improve response speed.
Solenoid Valve: Choose a reliable product to ensure proper operation.
Handwheel mechanism: In important occasions, it is recommended to avoid the use of handwheel mechanism to prevent human error.
Assembly supply: It is best to be provided by the manufacturer and assembly supply on the valve to ensure the reliability of the system and assembly connection.
Ordering information: When ordering, the detailed name, model, specification, input signal and output signal of the accessories should be provided.
Selection factors of control valves
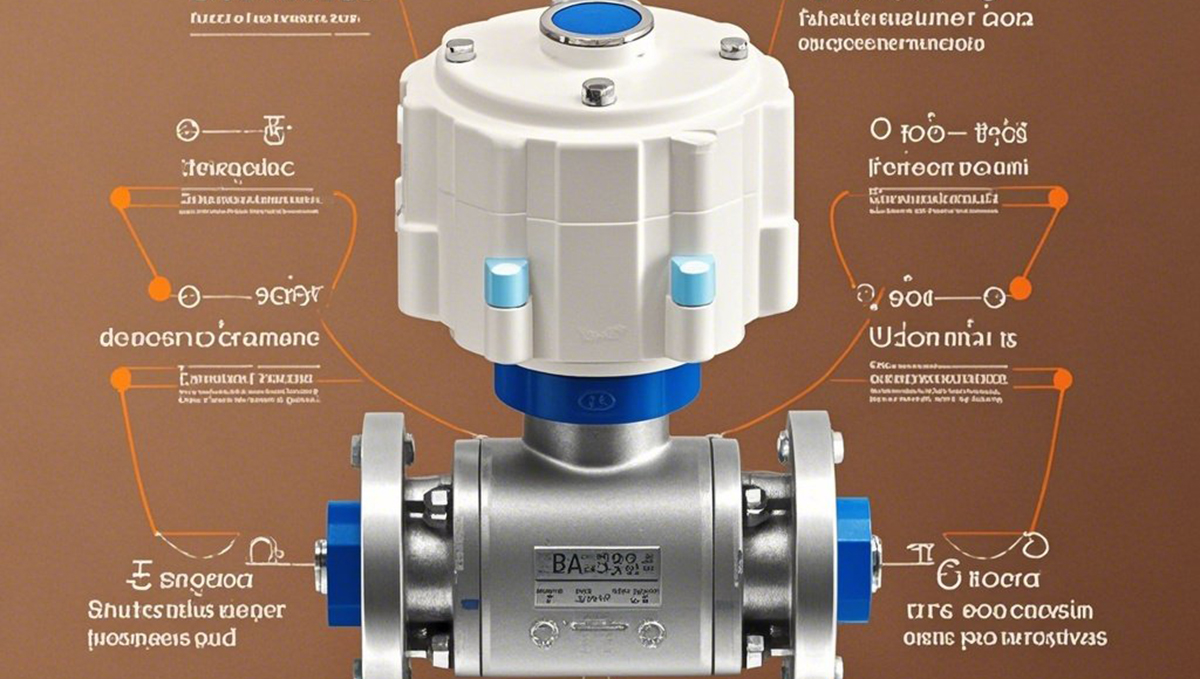