The three-break protection of pneumatic control valves (cut off gas, cut off power, cut off signal) is a key technology to ensure the safety of industrial systems. This article compares the two mainstream programs, analyzes its principle and application scenarios, to help you choose the optimal protection program.
First, the core function of three-break protection
Safety response mechanism
Disconnect gas / disconnect / disconnect signal: the valve is automatically fully open, fully closed or maintain the current position (position preservation).
Position preservation priority: to avoid loss of control of process parameters (such as high-temperature media valve position locking to prevent overheating).
Failure mode selection
Failure open (FO): suitable for scenarios requiring emergency pressure relief (e.g. boiler safety valves).
Failure closed (FC): suitable for preventing the leakage of media conditions (such as toxic gas pipeline).
Keep position (FL): to maintain the current state (such as chemical reactor temperature control).
Program comparison and working principle
Program 1: airlock valve + intelligent positioner (recommended)
Composition Working principle Advantages
Intelligent positioner (piezoelectric valve type) Automatically locks the position output when the signal/electricity is cut off, and the airlock valve cuts off the gas source to maintain the pressure balance. No need for external power supply, simple structure (50% fewer failure points)
Airlock valve Closes when the air source pressure is less than the set value, locking the diaphragm box pressure. Fast response time (<0.5 sec.)
Option 2: Signal Comparator + Directional Valve
Composition Principle of operation Limitations
Signal comparator Triggers the reversing valve when it detects a broken signal/electricity, simulating the logic of air break protection. Requires additional power supply, high complexity
Double-channel airlock valves Double-acting valves require double-channel airlock valves to maintain membrane chamber pressure. High maintenance cost (2-3 more accessories)
Third, the selection of key indicators
Environmental adaptability
High temperature / corrosive environment → Option 1 (no additional electronic components).
High precision control → Option 2 (signal comparator to enhance stability).
Response speed
Option 1: Response to gas failure <1 second, immediate locking of signal/electricity failure.
Option 2: Requires signal comparator processing, delay of about 0.5-1 seconds.
Cost Effectiveness
Option 1: Low initial cost (30% savings on accessories) and simple long-term maintenance.
Option 2: Suitable for complex systems (such as double-acting valves), but high maintenance costs.
Industry Application Cases
Petrochemical industry
Option 1: Pressure regulating valve at the top of atmospheric decompression distillation tower (position preserving function to prevent vacuum collapse).
Program 2: ethylene cracker fuel gas valve (fault shutdown to prevent flashback explosion).
Power industry
Scheme 1: Turbine bypass valve (keep open to protect the unit in case of gas break).
Scheme 2: Boiler feed water regulating valve (fault open to avoid dry boiler).
V. Maintenance and upgrading suggestions
Regular testing
Quarterly three-break simulation test (use pressure transducer to verify diaphragm box pressure).
Annual replacement of airlock valve seals (recommended Viton material).
Technical Upgrade
Remodeling of old system → add intelligent positioner (e.g. model with HART protocol).
High-risk scenarios → Option 1 + gas storage tank (extend hold time to 30 minutes).
Industry Standards and Certifications
IEC 61508: Functional safety standard (SIL 3 certification).
ISA 75.05: Control valve flow characteristics standard.
ASME B16.34: Valve pressure rating specification.
Summary
Pneumatic control valve three break protection program selection needs to be combined with process requirements and cost budget. Option 1 is recommended for most industrial scenarios due to its simple structure and high reliability; Option 2 is suitable for complex systems or high-precision control. It is recommended to contact a SIL-certified supplier for a customized protection solution. Regular maintenance can reduce the risk of unplanned downtime by more than 60% and ensure production continuity.
Pneumatic control valve three-break protection to achieve program comparison and selection guide
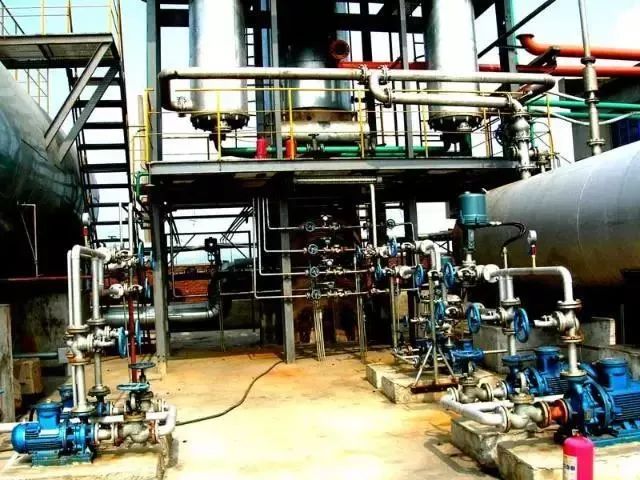