Thermal traps play a pivotal role in thermal systems, and their performance is directly related to the stability and energy efficiency of the steam system. As the core equipment of a steam system, the trap not only automatically removes condensate and prevents water hammer, it also prevents steam leakage and ensures the purity of steam and the continued efficient operation of the system.
However, the quality of traps on the market varies, with problems such as steam leakage occurring in newly purchased traps or steam leakage occurring after less than three months of use. These problems not only cause customers to complain, but also lead to a significant waste of steam resources.
Correct Installation of Traps Side-mounted Problems Description of the Problem: Mechanical traps should be installed horizontally, bimetal traps horizontally in principle but can also be installed vertically, and disc traps are installed at a more flexible angle. Failure to follow installation requirements, such as installing in the wrong direction or not using a bypass pipe, will result in a poor seal between the float and the orifice.
Solution: Be sure to follow the installation instructions and directions provided by the valve manufacturer to ensure that the trap can be easily accessed and replaced. Each brand of trap has its own specific installation method, and the instructions should be strictly followed when installing the trap.
Improper Selection Description of Problem: Selection is based on piping caliber as a criterion without taking into account the actual working conditions, and does not follow the principle of “trap capacity = steam-using equipment capacity × safety rate”.
Solution: Based on the capacity of the steam-using equipment and the appropriate safety rate, accurately calculate and select the appropriate trap model to ensure stable system operation.
Problem Description: Some traps are not designed with filtration in mind. After long-term use, impurities and scale tend to clog the air vent or drain holes, affecting condensate discharge.
Solution: Use traps with built-in filters to minimize the accumulation of impurities and scale and ensure smooth drainage. For example, some brands of traps are designed with a strainer in their internal structure. Damaged trap internals
Problem description: Internal components such as floats, orifices, and diaphragm boxes are damaged due to water hammer, wear and tear, corrosion, etc., causing the trap to leak. Solution: Select a trap with a water hammer prevention device, a flexible shut-off system, and a built-in strainer to minimize the risk of damage to internal components and extend service life. Inadequate Maintenance
Problem Description: Improper maintenance habits such as leaving bypass valves open for long periods of time and neglecting to check for trap leaks will result in wasted steam and reduced system efficiency.
Solution: Avoid leaving bypass valves open for long periods of time, and regularly use infrared thermometers to check temperatures before and after traps to detect and address leaks in a timely manner to ensure proper system operation and energy efficiency. By following these recommendations, you can ensure that your heat traps perform optimally in your steam system, improving system stability and energy efficiency.
Effective Troubleshooting After Trap Failure
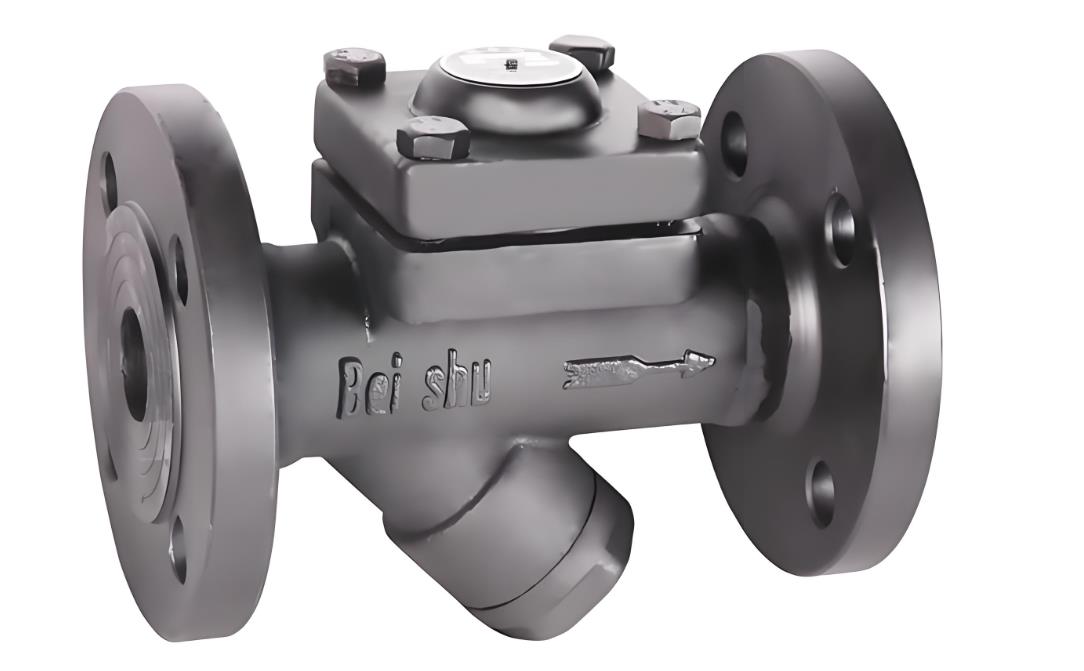