control valves play a vital role in industrial automation processes, however, they can also experience a variety of malfunctions that can originate from the valve itself, the actuator, the regulating mechanism or its accessories. For users, it is critical to understand the causes of these failures and solutions to ensure the smooth operation of the production line.
First, the main failure of the valve and the solution
Valve body and bonnet pressure parts
Failure: corrosion and wear, especially in corrosive fluids and high differential pressure conditions.
Solution: Regular inspection and replacement of damaged parts to ensure pressure strength and wear resistance.
Bolt
Failure: Looseness, uneven force or material incompatibility.
Solution: Tighten the bolts to ensure uniform force and use materials suitable for the working conditions.
Spool
Failure: Damaged by fluid impact, corrosion and particle impact.
Solution: Check and replace the damaged spool.
Valve seat
Failure: The sealing surface is corroded and damaged, resulting in leakage.
Solution: Inspect and replace damaged seats to ensure sealing performance.
Valve stem
Failure: Loose, worn or corroded connections to spool and push rod.
Solution: Tighten connections and replace worn or corroded parts.
Packing
Failure: Improper material, improper design, improper installation, or trapped debris.
SOLUTION: Replace with proper packing, install in correct manner, and remove debris.
Gaskets and O-rings
Failure: Rupture or aging.
Solution: Use high-temperature and corrosion-resistant wearing parts, and check and replace them regularly.
Failure of actuator
Pneumatic diaphragm actuator: Diaphragm not pressed, broken or sealing ring worn.
Solution: Press the diaphragm evenly, replace the damaged diaphragm, and replace the sealing ring.
Electric actuator: Short circuit, servo amplifier or motor failure.
Solution: Check the connecting wires and replace the damaged components.
II. Failures and solutions of regulating mechanism
Mismatch of flow characteristics
Failure: Control system is sluggish, oscillating or unstable.
Solution: Replace the appropriate regulating valve inner parts or regulating valve, or install the valve positioner.
Improper flow path design and installation
Failure: Increased noise, dirt accumulation, poor sealing.
Solution: Optimize the flow path design and reinstall the regulating valve to ensure proper flow direction.
Failure due to leakage
Failure: Internal leakage leads to decrease of adjustable ratio, external leakage causes environmental pollution.
Solution: Check the inner parts of the valve, replace the damaged parts, and make sure the flange is installed correctly.
Valve spool detachment
Failure: Control system mechanical noise increases, the controlled variable suddenly rises or falls.
Solution: Check the flow path of the regulating valve, replace the pin to ensure a firm connection.
Third, the pneumatic system common faults and solutions
Poor quality of gas source
Moisture: lead to component rust, pipe corrosion, poor action.
Solution: Set air trap at the outlet end of the compressor to remove condensate.
Oil: lead to seal deformation, action failure, environmental pollution.
Solution: Use oil removal filters, such as centrifugal filters or activated carbon adsorption.
Dust: leads to wear of components and malfunction.
Solution: Install air filter in the suction port of the compressor and clean or replace the filter element regularly.
Through the above detailed fault analysis and solutions, users can better understand and respond to the various problems that may be encountered during the operation of the regulating valve. This not only helps to improve production efficiency, but also reduces maintenance costs and ensures the continuous and stable operation of the production line.
Control valve failure analysis and solutions
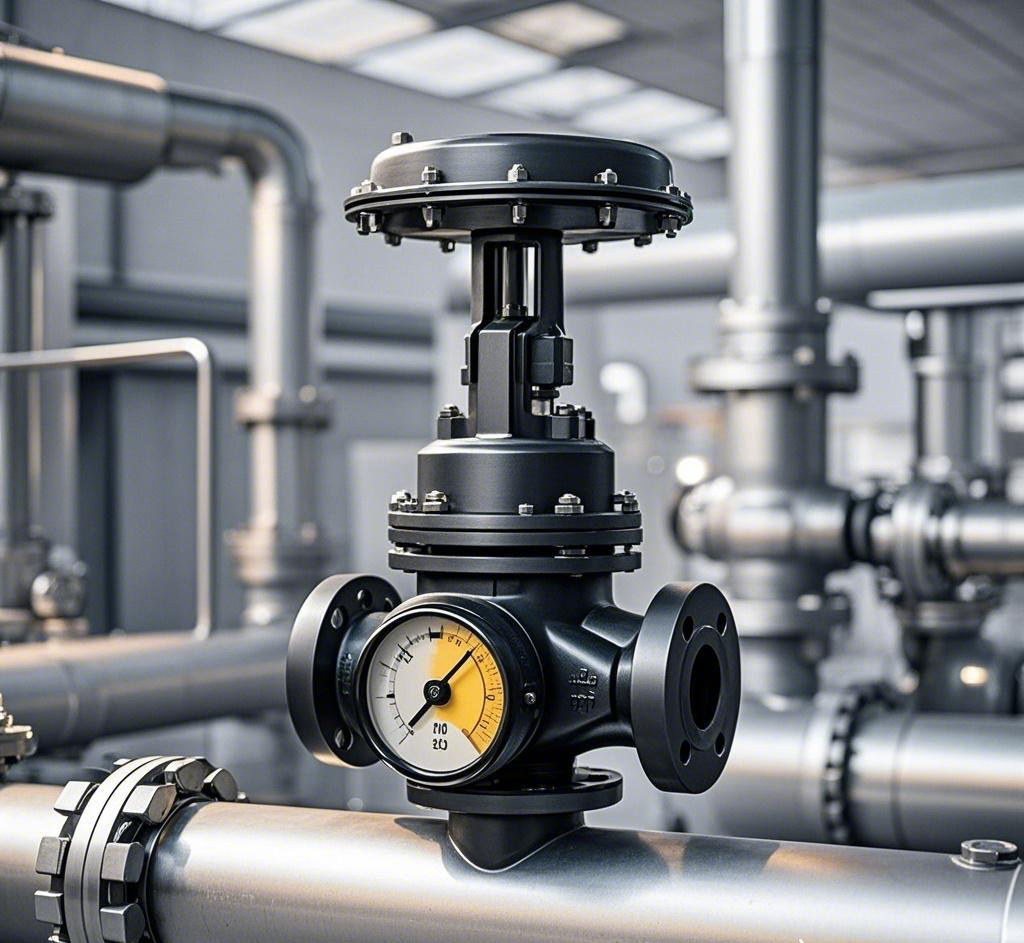