Actuators, the devices that drive valves, are becoming increasingly complex in design and function as technology advances. From simple human-operated gear sets to intelligent electronic components equipped with advanced control and measurement systems, actuators not only enable the switching of valves, but also monitor the operating status of valves and actuators to provide data for predictive maintenance.
Actuators utilize different forms of energy, such as electricity, liquids, gases, etc., and work under the command of control signals, which are converted into driving forces for linear or rotary movements. They can drive valves to the fully open or fully closed position, as well as precisely position the valve in any desired position.
Modern actuators incorporate a wide range of advanced features, including position sensing, torque sensing, electrode protection, logic control, digital communication, and PID control, all of which are compactly housed in a single enclosure. They not only serve as an interface between the control system and the mechanical movement of the valve, but also enhance operational safety and environmental protection performance.
When selecting an actuator, the first consideration is the type of valve and the operational requirements. Rotary valves (e.g., plug valves, ball valves, butterfly valves) require actuators capable of 90-degree rotary operation with the required torque, while multi-rotary valves (e.g., Globe valves, gate valves) require multi-rotary operation to drive the valve to the open or closed position.
There are four main types of actuators:
Electric multi-turn actuators: use single-phase or three-phase motors to drive gears or worm gears, and ultimately drive the stem nut to produce movement in the valve stem. They are compact and full-featured, but the valve can only remain in place when the power fails.
Electric single-turn actuators: Similar to electric multi-turn actuators, but the output is 1/4 turn (90 degrees) motion. They are compact, suitable for small size valves, and can be battery operated for fail-safe operation.
Fluid Driven Multi-Turn or Linear Output Actuators: Commonly used to operate straight-through valves (globe valves) and gate valves, using either pneumatic or hydraulic operation. They are simple, reliable, and easy to implement fail-safe operation modes.
Fluid Driven Single Rotary Actuators: Pneumatic and hydraulic single rotary actuators are very versatile, require no power, are simple and reliable. They use cylinders and actuators to convert linear motion to right-angle outputs, and actuators usually have toggles, rack and pinion, and levers.
When selecting an actuator, the following elements should also be considered:
Drive energy: The choice of power or fluid source depends on the specific application. Electric actuators have a wide range of power supply types to choose from, while fluid sources can be compressed air, nitrogen, natural gas, hydraulic fluids, etc.
Valve type: Know the type of valve in order to select the correct type of actuator. For example, some valves require multi-turn drives, some require single-turn drives, and some require reciprocating drives.
Torque Size: Obtain the torque size of the appropriate valve through the valve manufacturer in order to select the proper actuator specifications.
Actuator Selection: Once the type of actuator and the required drive torque for the valve have been determined, the actuator can be selected using the data sheet provided by the actuator manufacturer or the selection software.
In addition, actuators can be used for on-off control and continuous control. Switching control allows the operator to operate the valve from a distance, while continuous control requires the actuator to actuate frequently to control parameters such as level, flow or pressure in the process system. Digital communication systems can transmit commands and gather information quickly and efficiently, reducing installation costs and providing a wealth of valve information for predictive maintenance.
Predictive maintenance uses the built-in data memory to record the data measured by the torque sensing device each time the valve is actuated to monitor the status of the valve’s operation and predict failures. This data is invaluable to the valve’s maintenance program, helping operators to identify and resolve problems in a timely manner.
Control valve (control valve) how to choose the actuator
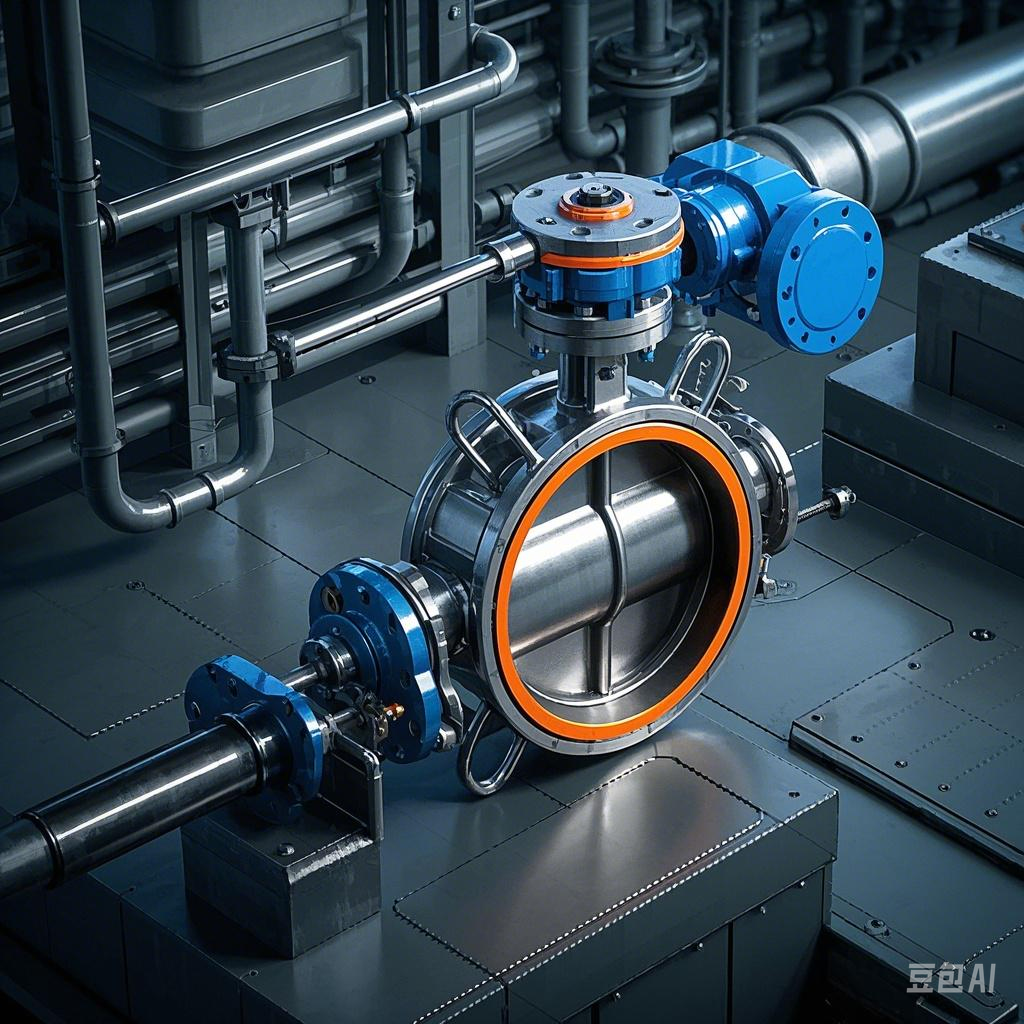