Pneumatic valve, an efficient and flexible fluid control device, is widely used in various industrial automation systems. It uses compressed air as a power source through a cylinder as an actuator to drive the valve on and off, realizing the precise adjustment of temperature, flow, pressure and other parameters in the pipeline. In this paper, we will introduce the working principle of pneumatic valves, significant advantages and solutions to common failures.
First, the working principle of pneumatic valve
The core components of pneumatic valves include pneumatic actuators, valve bodies and accessories. The actuator utilizes components such as spring, diaphragm/piston, and pneumatic rod to receive a gas signal of 20 to 100kPa or an electrical signal of 4 to 20mA, converting clean compressed air into mechanical power to push the valve body into action. The valve body is internally composed of valve flap, valve cage and valve stem, etc. The precise control of flow is realized by adjusting the flow area between the spool and the valve seat.
When the regulator room input 0.02 ~ 0.10MPa pressure signal, the film produces thrust, pushing the thrust disk to compress the spring, which in turn drives the valve stem, the push rod and the spool to move, complete the opening or closing action of the valve.
Second, the advantages of pneumatic valve
Pneumatic valve with its unique advantages, in the field of industrial automation occupies an important position:
Fast response: pneumatic valve action quickly, can be completed in a very short period of time to adjust the instructions, improve production efficiency.
Powerful thrust: with the use of large cylinders, can produce a large torque propulsion, to meet the needs of a variety of complex working conditions.
Stable and reliable: in a variety of harsh environments, pneumatic valves can still maintain safe and stable operation for a long time, reducing maintenance costs.
Third, the common faults and solutions of pneumatic valve
Increase in leakage
Reason: spool wear, foreign matter in the valve, the media pressure difference caused by the decline in rigidity.
Solution: replace the new spool, clean the valve foreign matter, improve the actuator to increase the air source. Ensure that the length of the valve stem is appropriate during installation to prevent the valve from not closing completely.
Action is not stable
Reason: signal pressure or air source pressure is not stable, positioner failure, output pipe or line is not tight.
Solution: Ensure the power network is stable, readjust the positioner or replace it with a new one, add lubricant to reduce friction, adjust the precision of the positioner’s output pipe position.
Vibration
Cause: Bushing and spool friction, vibration equipment around, the base is not stable, improper installation direction.
Solution: Replace the bushing, eliminate the source of vibration, replace the new base, adjust the pneumatic Valve Installation direction.
Slow action
Reason: Diaphragm damage, packing abnormality, dust inside the valve body, stem friction.
Solution: Replace the new diaphragm, check and replace the packing, clean the valve body of foreign objects, reduce stem friction.
No action
Reason: No air source or output of positioner, faulty command line, deformation of valve spool and valve stem.
Solution: Check the command line to eliminate faults, replace the positioner with a new one, replace the spool and stem with a new one, and make sure the handwheel is properly positioned.
Through the above introduction, readers can more intuitively understand the working principle of pneumatic valves, advantages and solutions to common failures. In the actual application, when encountering pneumatic valve failure, can be based on the above program to troubleshoot and repair, to ensure the normal operation of the equipment and production efficiency.
Pneumatic valve: working principle, advantages and common failure solutions
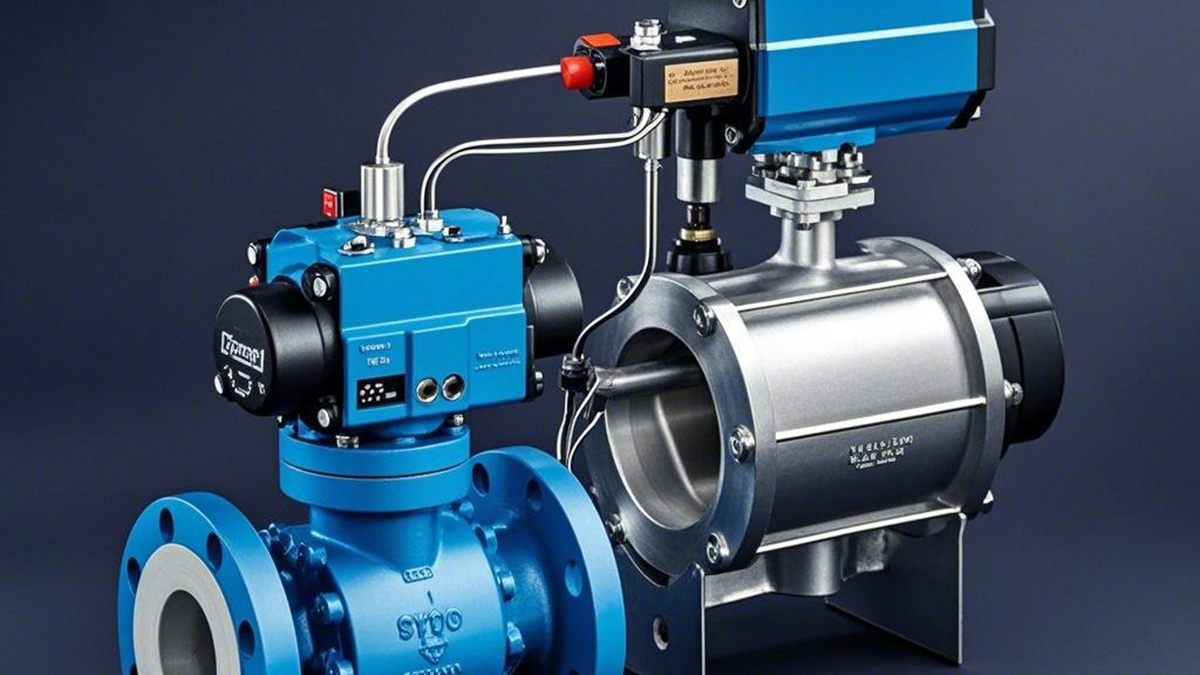