valve assembly is a crucial part of the manufacturing process that determines the final performance and reliability of the valve. This step is based on well-defined specifications that precisely combine the parts and components of the valve to form a complete product.
Complete machine and assembly basis
The complete machine is the basic unit of Valve assembly and consists of a number of parts that make up the components of a valve, such as bonnets and flaps. The process of assembling these parts into components is called component assembly, while the step of further combining parts and components into a complete valve is called total assembly. Assembly work on the quality of the valve has a decisive impact, even if the design and parts are flawless, if the assembly is not appropriate, the valve may not be able to meet the specified requirements, and even seal leakage and other problems. Therefore, a reasonable assembly method must be used to ensure the final quality of the valve.
Common methods of valve assembly
There are three main methods of valve assembly: complete interchange method, selection method and repair method.
Complete swap method
Complete interchangeable method of assembly of valves, each part does not require any trimming or selection, can be directly assembled, and the assembled product to meet the technical requirements of the regulations. At this point, the valve parts must be strictly in accordance with the design requirements for processing to meet the requirements of dimensional accuracy and positional tolerance. The advantage of this method is that the assembly work is simple, economical, the technical requirements of workers are not high, high production efficiency, easy to organize the assembly line and specialized production. However, it requires high machining accuracy of the parts and is suitable for valves with relatively simple structure, such as Globe valves, check valves and ball valves, as well as valves with small and medium diameters.
Selection and matching method
Selective fitting method assembly of valves, parts can be processed according to the economic accuracy, assembly and then a certain size with adjustment or compensation function for selection, in order to achieve the specified assembly accuracy. This method adjusts the size of the compensation ring by selecting fittings of different sizes to achieve the required assembly accuracy. For example, in a double-gate wedge gate valve, the assembly accuracy of the valve can be ensured by adjusting the thickness of the top core and the regulating gasket. In order to ensure that the fixed compensation parts can be used for selection in different situations, it is necessary to premanufacture a set of compensation parts such as gaskets and bushings of different thicknesses for assembly.
Repair method
Repair method of assembling valves, parts can also be processed according to the economic accuracy, assembly and then have to adjust or make up for a function of the size of the repair. For example, in the wedge gate valve, due to the realization of interchangeable requirements of the higher processing costs, many manufacturers have adopted the repair method process. When grinding the gate sealing surface to control the opening size, it needs to be adjusted in conjunction with the opening size of the valve body sealing surface to achieve the final sealing requirements. Although this method increases the matching plate process, but greatly simplifies the dimensional accuracy requirements of the previous processing process. Matching plate process is operated by specialized personnel, skilled, so it does not affect the production efficiency.
Valve assembly process
Valve assembly is usually carried out in a fixed site, zero, parts assembly and total assembly are completed in the assembly plant. The required parts and components are shipped to the assembly workplace in advance. In order to improve the assembly efficiency and quality, parts assembly and general assembly are usually carried out by several groups of workers at the same time. This not only shortens the assembly cycle, but also facilitates the use of specialized assembly tools, and the technical requirements for workers are relatively low.
Some foreign high-end valve manufacturers also use assembly suspension line or assembly rotary table mode of assembly.
Preparation before assembly
Before assembly, the valve parts need to remove the burrs generated by machining and welding residues of welding slag, and cleaning and preparation of packing and gaskets.
Cleaning of valve parts
Valves, as fluid line control devices, must have clean internal cavities. Especially nuclear power, medicine and food industry valves, the purity of the medium and prevent media contamination requirements are more stringent. Therefore, before assembly, the valve parts must be cleaned to remove chips and debris, residual slick oil, coolant, as well as burrs, welding slag and other dirt. Cleaning is usually done by spray brushing with alkaline water or hot water, or in an ultrasonic cleaning machine. After the parts have been ground and polished, a final cleaning is required. Final cleaning usually involves brushing the sealing surface area with gasoline, then blowing it dry with compressed air and wiping it clean with a cloth.
Preparation of packings and gaskets
Graphite packings are widely used because of their corrosion resistance, good sealing properties and low coefficient of friction. Packings and gaskets are used to prevent leakage of media through the stem and bonnet as well as the flange union. These fittings need to be cut and collated ready before valve assembly.
Valve assembly process
Valves are usually based on the valve body as a reference part, in accordance with the order and method of assembly process regulations. Before assembly, parts and components should be inspected to ensure that there is no un-burr and uncleaned parts into the
Valve assembly: the final step in ensuring product quality
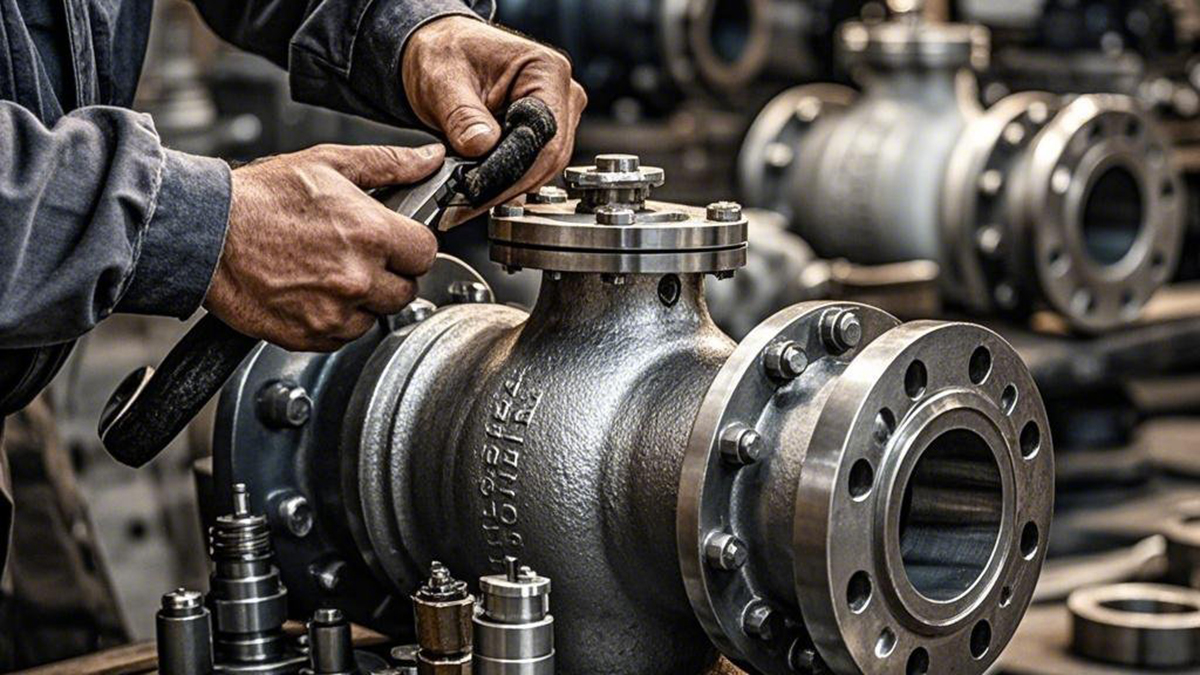