Pneumatic control valve, this compressed air as a power source of precision equipment, through the cylinder actuator and valve positioner, converter and other auxiliary components, to receive industrial automation control system commands, accurately adjust the pipeline medium flow, pressure, temperature and other key process parameters. In the petrochemical, electric power, metallurgy and other process industries, pneumatic control valves play an indispensable role. Therefore, it is crucial to ensure its stable and reliable operation. Once a failure occurs, rapid and accurate troubleshooting and repair is essential to maintain the smoothness of the production line.
First, the troubleshooting of gas source problems
The normal operation of the pneumatic control valve depends on a stable gas source. The following are some common air source failures and their solutions:
The gas source is not turned on: Check whether the gas source switch on the site has been turned on.
Air supply contains water and freezes: In cold weather, make sure the air supply is dry to avoid water freezing and causing malfunctions.
Interruption of purified air supply: Monitor the status of purified air supply to ensure continuous stability.
Low air pressure: Check whether the air source main pipe is leaking or the air line is blocked to ensure that the air pressure reaches the required standard.
Failure of air filtration pressure reducer: Clean the pressure reducer regularly to avoid the accumulation of dirt, resulting in insufficient output air pressure.
Air leakage from the air line on site: check whether the joints of the air line are loose and ensure good sealing.
Filtration pressure reducing valve failure: Regularly check and maintain the filtration pressure reducing valve to ensure its stable performance.
Second, line failure diagnosis
Line faults may lead to fluctuations or interruptions in the signal received by the pneumatic control valve. The following are some common line faults and their troubleshooting methods:
Loose or detached terminals: Check whether the power line terminals are tight to avoid poor contact.
Water and moisture in the equipment: After bad weather, check the equipment for moisture and make sure the wiring is dry.
Reversed polarity: Make sure the polarity of the power cord is correct to avoid inactivity of the regulating valve.
Wire Failure: Check the wire insulation regularly to make sure it is in good condition to avoid short circuit or breakage.
Wiring error: After maintenance, make sure the wiring is correct to avoid regulating valve failure.
Signal instability: check whether the output signal of the regulating valve is stable to avoid operational fluctuations.
Third, the positioner fault handling
The positioner is one of the key components of the pneumatic control valve. The following are some common positioner faults and their solutions:
Loose or detached feedback rod: Check whether the feedback rod fixing nut is tight to avoid oscillation caused by loose or detached feedback rod.
Position sensor failure: regularly replace the aging position sensor to avoid abnormal display in the center control room.
Improper adjustment of PID parameters: adjust the PID parameters of the positioner according to the actual demand to ensure stable performance of the control valve.
Fourth, the repair of control valve valve body failure
Control valve valve body failure may directly affect its regulatory performance. The following are some common valve body failure and its repair method:
Spool or seat wear: regularly replace the worn spool or seat to avoid media leakage or jamming.
Packing pressure is too tight or too loose: adjust the packing tightness to ensure that the regulating valve moves smoothly and seals well.
Installation is not concentric: Ensure that the pipeline and the valve body are concentric during installation to avoid additional stress leading to oscillation.
Loose fixing nut: Check and tighten the fixing nut regularly to avoid high frequency oscillation or breakage of the valve stem.
Diaphragm head failure: regularly replace the aging diaphragm and compression spring to ensure stable performance of the control valve.
In summary, the stable operation of pneumatic control valves is crucial to the smoothness of industrial automation systems. Through regular maintenance and troubleshooting, you can ensure that the pneumatic control valve is always in the best condition, providing a strong guarantee for the stable operation of the production line.
Pneumatic Control Valves: A Key Component for Industrial Automation and Its Maintenance Guide
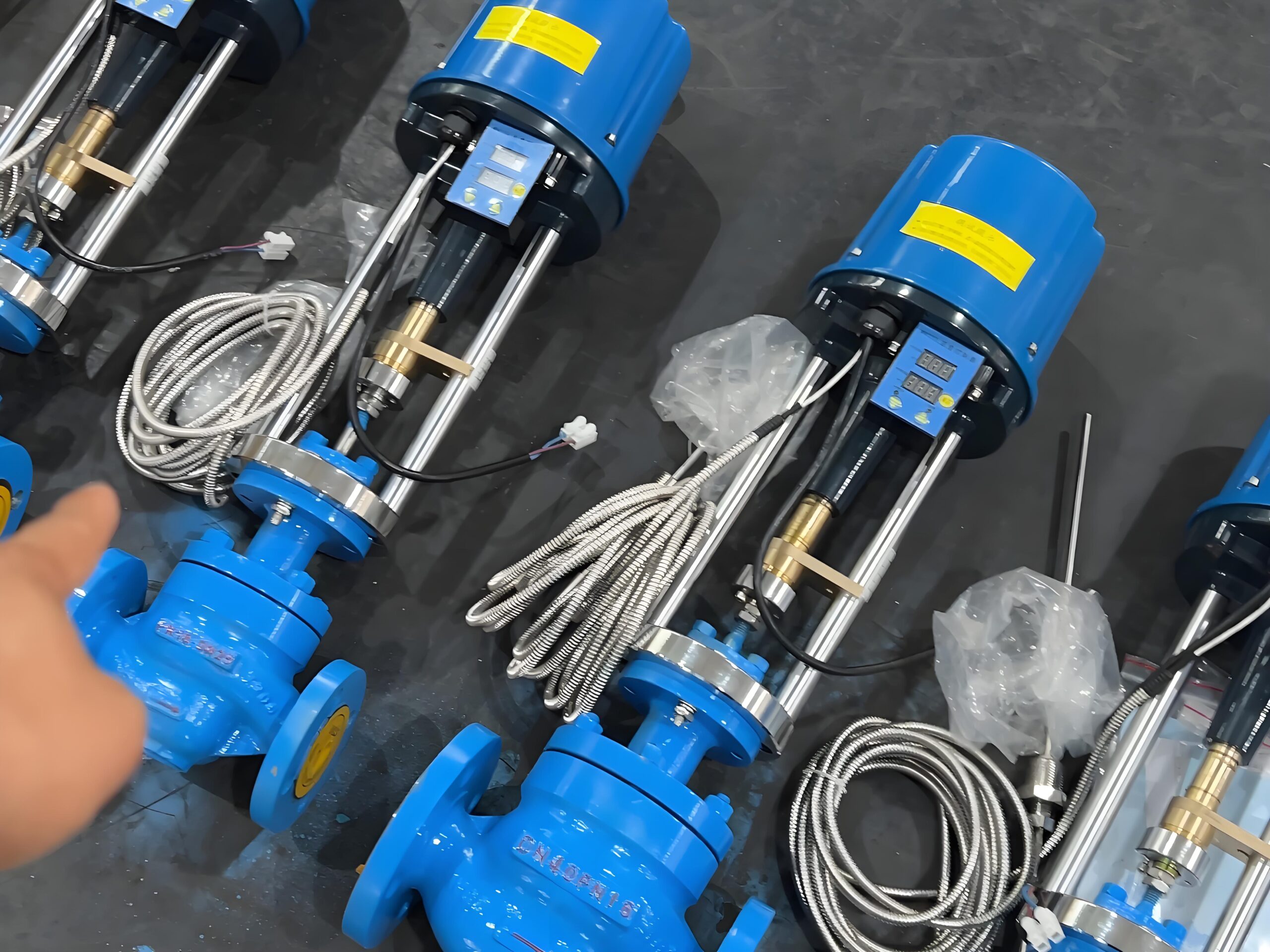